The impact that technology and data exchange is having on workplace safety is both fascinating and exciting, but what must we do to meet the inevitable challenges to come?
Features
We are only human
Commonly known as Industry 4.0, the current trend of automation and data exchange in manufacturing technologies, is having an effect in the field of human factors and safety performance. Without doubt, there are major positives for safety, as better engineering tech helps keep workers out of harm’s way.
Already, there is smart personal protection equipment (PPE) that actively identifies hazards such as temperature changes, sudden movement or potentially concerning inactivity. Smart surveillance systems that use CCTV and PPE recognition software to ensure people are wearing what they should, where they should, also exist.
Such ‘better, cheaper, safer, more reliable’ logic will also eventually apply to less-hazardous manual tasks for which automation has traditionally been unaffordable. There are clear long-term health benefits to be had too, with fewer incidents of harm due to repetitive work. It is possible as well that many of the most hazardous jobs will simply disappear. But, as we shall see below, this does not mean that we can lessen our efforts to increase safety; in fact, with new technology come new challenges that require a renewed focus on human factors.
Speedy evolution – not true revolution
When it comes to job numbers, experts are divided on the long-term impact of automation. In the past, technological advances have ultimately increased the aggregate number of jobs in the economy, but with different kinds of jobs coming on stream.
As Industry 4.0 comes to pass, people will clearly still be needed to design, build, install, run and maintain the new technologies; new industries will also appear that we have yet to imagine.
However, most experts agree that, despite the faster rate of change, over the next 10 years or so we will not see a radical, overnight shift in the employment landscape. We will still need people to negotiate existing hazards and deal with the coming changes and hazards that the workplace of the future will bring.
So, what will cause injuries in the future? The same things that cause injuries now. There are only three possible reasons why people get hurt. Either you do something that leads to your own injury (the most common), the ‘other guy’ does something that leads to you getting hurt, or a non-human event, such as equipment breaks or a hazard, occurs that leads to an incident.
Very often, when people get hurt in the workplace it is during everyday activities such as walking, using the stairs, or encountering objects, other people or moving equipment/vehicles. These are eventualities that one cannot engineer out of existence or easily guard against.
Companies typically reach a plateau at which doing more of what they have done in the past, the things that significantly reduced injuries over the longer term, loses some of its effectiveness. Technology may eventually move us beyond that plateau, but until we get to that stage of airbag-deploying workwear that senses a fall as it is happening, these types of injury will persist.
Critical states of mind
Why and when do people get hurt? For the vast majority, it is about states of mind or body such as rushing, being frustrated with a situation, being tired or fatigued or simply having done something so often for so long that we become complacent and go on autopilot.
We are hardwired to function subconsciously the vast majority of the time. Thus, complacency becomes pervasive once we get used to doing something. Indeed, technology can even exacerbate complacency: if we rely only on technology to keep us safe, what happens when it fails or is absent?
The four critical errors
From a safety point of view, we can simplify mistakes into four critical errors: eyes not on task; mind not on task; putting oneself in the line of fire or losing balance, traction and grip. These four errors account for over 90 per cent of all injuries — and a lot of other non-safety mistakes too. If we assume that there are a mere four errors in play and those errors are most likely to happen when we are in one of four states, the problem of reducing error becomes easier to tackle – and with it the chance to reduce injury levels.
Error reduction and new skills
To reduce critical errors, therefore, we can ingrain new skills and habits that will account for these states and allow us to avoid making critical errors. Using the same types of neural pathway that make us go on autopilot, we can give our brains failsafe techniques for when we are most likely to make an injury-causing error.
One of the first techniques we get people to practice is to observe those around them. If we see someone in one of the four states – rushing, frustrated, and looking tired or on autopilot – it helps us to bring ourselves into the moment, keep out of harm’s way and also reflect on our own actions.
Another good technique is to reflect on the small mistakes that we make and look for a link to one of the four states. Such reflections can turn out to be hugely consequential.
It is also possible to help people recognise when they are in one of the first three states: rushing, frustration and fatigue (combating complacency requires a different approach). The breakthrough comes when people learn to both amplify and listen to their own inner voice telling them that something feels wrong. We call this technique self-triggering, which is catching oneself in one of those states before an error or injury occurs.
All this takes time and practice and will become, if anything, more relevant as technology’s impact grows and new equipment and industries become a reality.
Whatever happens, the human factor will remain critical in Industry 4.0. Alongside advancing engineering and technological solutions that address risk, we will always need to help people develop the personal safety skills that allow them to deal with the new world, whatever that ends up looking like.
read our report on Future Risk at: britsafe.org/campaigns-policy/future-risk/report
David Hughes
Development director (UK, Ireland and Nordic countries)
SafeStart
FEATURES
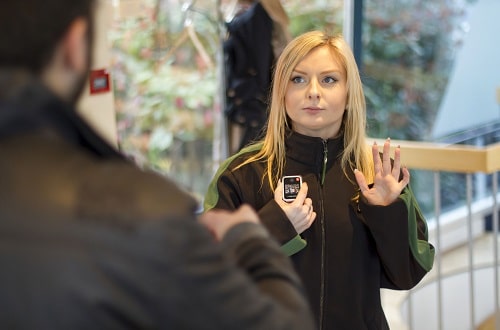
Purchasing body-worn cameras: 10 top tips
By Alasdair Field, Reveal Media on 13 May 2024
Body-worn cameras can reduce the risk of violence and threats to staff by providing a deterrent effect and documentary evidence for pursuing aggressors, but it’s important to carefully consider issues like functionality, data storage and user training during the selection process.
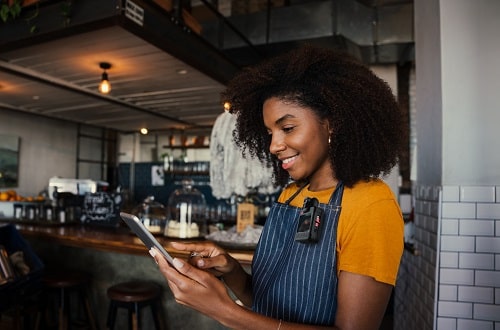
Vulnerable workers: protection is key
By Naz Dossa, Peoplesafe on 13 May 2024
From working alone to commuting after hours, workers can be vulnerable to threats, aggression and harassment – but training and the right technology can help.
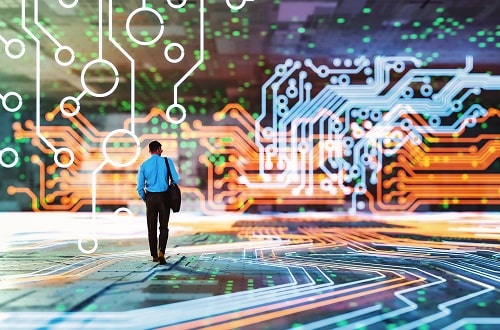
AI and worker wellbeing: a new risk for employers
By David Sharp, International Workplace on 10 May 2024
Data generated by machine learning and artificial intelligence at work looks set to play a huge role in boosting both worker health and safety and business productivity, but it’s vital that workers’ data used for algorithmic processing is handled lawfully, fairly and transparently.