Employers often wrongly assume that noise control techniques for machinery are both costly and impractical. In fact, simple, very low-cost engineering modifications that anyone can implement are often all that are required – and they may even be self-financing.
Features
Preventing hearing damage and cutting costs: practical noise control is key
It’s a sad fact that the general standard of advice on reducing the risk of hearing damage to workers in environments such as factories, workshops and foundries is abysmal and, consequently, many people continue to suffer unnecessary hearing damage.
The noise consultancy industry is predicated on measurement (such as measuring noise levels from machines and taking measurements in an attempt to estimate workers’ personal noise exposures), typically recommending nothing other than providing personal protective equipment (PPE), like ear defenders, as risk mitigation.
Photograph: iStock/CasaraGuru
This is exactly the opposite of the hierarchy of control (HoC) requirement that noise control should be the priority. In fact, the Environment Agency recently published the results of a survey of the quality of reports from noise exposure control consultants, 95 per cent of which were deemed inadequate, and 60 per cent as “extremely poor”. An earlier Health and Safety Executive (HSE) survey of occupational noise risk mitigation reporting produced similar results.
The current approach has failed to prevent extensive unnecessary hearing loss among workers. Organisations are unwittingly wasting resources on measures that are not best practice and not sufficiently effective. This article details the failings and provides a guide to using modern noise control technology to make noise risk reduction much more effective within current budgets.
As the Control of Noise at Work Regulations guidance states that “these regulations are concerned with controlling noise, not measuring it…”, companies must evaluate their noise control options and not just repeat placebo risk assessments that inform them of what they already know with no useful information on noise control.
The ‘hierarchy of control’ for noise – conspicuous by its absence…
The measurements of noise risk provided in reports may be reasonably accurate. However, the risk management recommendations are almost invariably woefully inadequate. Typically, they are just evaluations of PPE performance based on unrealistic expectations of the real-world protection offered by ear defenders and ear plugs. There may also be a statement that amounts to “it would be a good idea if you could work out a way to reduce noise levels somewhat, here are some copy-and-pasted generalisations re. noise control”.
Hearing protection should be ‘first aid’ until noise exposure can be reduced, not ‘the permanent and only aid’, particularly when HSE research proves that it typically only provides adequate protection up to noise doses of 83dB(A) to 90dB(A). Under the Control of Noise at Work Regulations, PPE can only be used as a long-term measure if you can prove that noise levels cannot be reduced. Proving this requires a Noise Control Audit (NCA) to generate a cost/benefit analysis of the noise control options for plant and machinery based on the best current available technology. An NCA will provide information on the cost of the noise control technology and by how much it will reduce the exposure risk. The cost of the technology can then be compared with factors like savings from lower PPE expenditure, a reduction in employees’ noise exposure and improved working conditions to identify the most appropriate noise control technology to invest in.
Have any of your previous noise reports included an NCA? I thought not…
Consequently, most organisations make expensive, uninformed decisions regarding noise-induced hearing loss (NIHL) reduction programmes based on inadequate information in reports.
The HoC is the basis for determining the most effective and practical noise risk reduction programmes. Figure 1 below compares the HoC with the inverted version recommended in virtually all noise risk management reports.
Figure 1: Hierarchy of Control versus the inverted noise version. Credit: INVC
The two extremely common misunderstandings that result in the prevalent poor risk management recommendations are:
- Assuming that PPE is massively more effective than the reality. The prevailing attitude of ‘PPE issued, problem solved’ is not correct and is not acceptable.
- Assuming that noise control is very costly and not practical when modern techniques can often be self-financing.
- In both cases, the problem is a lack of knowledge on the part of the report writer.
The health and financial costs of ignorance
Health¹
- Dementia: mild NIHL doubles the risk of dementia, while severe NIHL increases the risk by a factor of five times. Hearing loss in middle age increases the dementia risk by nine per cent and is the highest modifiable risk factor for the condition.
- Employment: employment rates in young males with NIHL are 30–40 per cent lower than men of the same age without NIHL and NIHL results in an increased rate of early retirement in older people.
- Accident-related injuries: high levels of NIHL doubles the rate of injury.
- Mental health: NIHL has been linked to higher rates of depression and loneliness; high levels of NIHL are comparatively a higher risk for mortality than obesity or physical inactivity.
- Household income: decreases with severity of NIHL.
Financial
It is estimated that hearing damage due to noise exposure at work currently costs the UK economy around £25 billion each year. The costs for an organisation include:
- Costs due to the increased number of accidents caused by NIHL.
- Reduced productivity, absenteeism, staff turnover.
- NIHL hearing damage compensation claims.
- Insurance cost: where there is a risk of NIHL at work, part of an employer’s insurance premium cost will be related to the perceived risk of NIHL.
- Cost of PPE: capital, maintenance and administration costs are in the region of £200 –£600 (or more) per head per annum for a measure that typically reduces the risk by only 50–90 per cent.
- Audiometry for those exposed to a noise dose above an 85dB(A).
- Repeated (often placebo) noise surveys.
There is enormous variation in these per capita NIHL risk management costs for different organisations. It is a very useful (and often salutary) exercise to spend a few minutes generating rough cost estimates for each of these factors. Is the cost per 50 staff around £10,000 per annum (pa) or closer to £50,000 pa? Compare this cost with the calculated risk reduction. Is that good value? Much of those resources could almost certainly be better spent on measures to reduce the risk of an almost 100 per cent preventable condition.
What actions should you take?
- Estimate your current total budgetary spend (as above) on noise exposure risk management and estimate the reduction in risk that is being achieved in practice. (This involves calculating the real-world performance of the PPE. Real-world means the actual level of protection when PPE is worn at work, compared with the PPE manufacturer’s official data on the noise reduction – or attenuation – theoretically provided, taking into account factors that will affect the level of attenuation, such as poor fitting of the PPE and poor wear rates among employees).
- Update PPE programmes to increase efficacy in the short term – click here for advice from INVC on how to achieve this.
- Carry out a Noise Control Audit (see below) to generate a real-world cost/benefit analysis of the noise control options using the best of current technology. This is a regulatory requirement.
- Use steps one and three to estimate the pay-back period for an effective noise control programme. Factors to consider include avoiding the need for audiometry (the provision of regular hearing checks for workers at risk of NIHL due to noise exposure at work; reducing or eliminating PPE use, avoiding the need for further noise surveys; and lower insurance premiums, etc.
- Implement the cost-effective elements in the noise control programme.
- Re-assess noise levels and revise the hearing conservation programme accordingly.
The Noise Control Audit (NCA) – mandatory under the regulations
When employers have a noise problem at work, the discussion and thought-process about how to reduce the risk often follows this pattern: “Let’s discuss noise control at the regular health and safety meeting. The quotes for the generic acoustic enclosures aimed at separating noisy machines from the workforce suggested in the noise report are exorbitant, the maintenance engineers would hate them, and it would make hygiene and cleaning a nightmare. So, they’re not practical. Next topic please…”
Mention ‘noise control’ and the almost universal kneejerk reaction is to imagine high-cost acoustic enclosures, barriers and silencers that can interfere with plant operation and productivity. These traditional techniques are not the only options. In a surprising proportion of projects, simple, very low-cost engineering modifications that anyone can implement are all that are required – see the INVC website for examples. These can even be self-financing. The problem is a lack of knowledge leading to false assumptions about the costs and benefits of noise control.
I have been involved in engineering noise control for decades. I can walk through virtually any noisy site and provide an instant evaluation of the noise control options for most items of plant.
For example: “Machine 1: easy, circa £300, 10dB reduction; easy, c. £2,000, will reduce noise below 80dB(A). Line 1: moderately difficult, but once you’ve done the first one, you can copy the noise reduction controls to the other lines at around £3,000 per line. This will result in a 7dB(A) reduction, reducing noise levels below 85dB(A). Machine 2: impossible, the only option is an enclosure that would not be practical. I’ll provide you with a “you are doomed” certificate so you can use PPE in perpetuity...”
That is the principle of an NCA. A knowledgeable engineer makes detailed diagnostic measurements on each type of machine and discusses the practicalities with company engineers. They can then determine both the reduction in noise level that can be achieved and the implementation cost using a local engineering contractor. This provides the accurate cost/benefit analysis required to make informed decisions about the optimum effective hearing conservation programme for the site.
Alternatively, an in-house engineer with some knowledge and the help of Google can make preliminary evaluations. There are extensive online resources published by the HSE, INVC (search the largest online database of engineering noise control case studies in the world) and others. Or send a smartphone video clip and some noise data to us at INVC for an initial evaluation of the options.
A Noise Control Audit should be carried out instead of a repeat risk assessment (saving the associated costs) or appended as an update to a conventional noise survey. Payback periods of a year or so are not uncommon – see INVC’s website for examples.
It is important to understand that even if PPE would still be required post-noise control, reducing the noise level from perhaps 93dB(A) down to 88dB(A) means that the risk has been reduced by 70 per cent and that PPE is more likely to be effective.
Example – Noise Control Audit cost/benefit analysis
Financial benefits
This table shows the results of an NCA for the key noise sources at a high-hygiene food industry site:
Source: INVC
It predicts the noise reductions and costs involved to implement noise control on the major noise sources.
In addition, the real-world performance of the PPE in use is evaluated (see table):
Source: INVC
This shows that the 50 staff using the earmuffs are achieving an average of 5dB attenuation in practice at a cost of £180 per head per annum in direct costs. However, this is not sufficient to eliminate NIHL risk.
The total annual hearing conservation programme costs for the area are estimated at £15,500 from the following table:
Source: INVC
This information is then combined to generate the cost/benefit analysis shown in Figure 2. This indicates that, compared with continuing with the PPE-based approach, the noise control programme would pay for itself in less than two-and-a-half years. Thereafter, it would save around £13,000 per annum with reduced administration, policing and other resources.
Figure 2: Cumulative PPE Programme v Noise Control Costs. Source: INVC
Health benefits
The Noise Control Audit results in this example indicate that the highest noise level to which operators could be exposed would be 83dB(A) and that, based on the noise assessment results, all operator doses would be well below 80LEP,d. Consequently, there would be no risk of hearing damage into the future, and there would also be significant improvements in communication and working conditions due to removing the requirement to wear hearing protection.
Noise Control Audits: the missing regulatory requirement that cuts risk and costs
The current approach to noise risk management has failed to prevent unnecessary hearing damage for millions. This is due in large part to a lack of understanding of the real-world limitations of PPE performance coupled with woeful ignorance on the part of report writers when it comes to noise control.
Carrying out a Noise Control Audit to generate a cost/benefit analysis of the control options is a mandatory requirement of the Noise at Work Regulations that cuts both costs and the risks of hearing damage. Such audits are currently very conspicuous by their almost total absence. It’s time to change...
Peter Wilson is technical director at Industrial Noise and Vibration Centre (INVC)
Online resources:
Click here for a comprehensive list of online resources from a variety of organisations.
For more information see: invc.com
T. +44 1753 698 800
References:
- Sources: Deloitte Access Economics 2017a. Lin et al 2018. Lancet Commission 2017
FEATURES
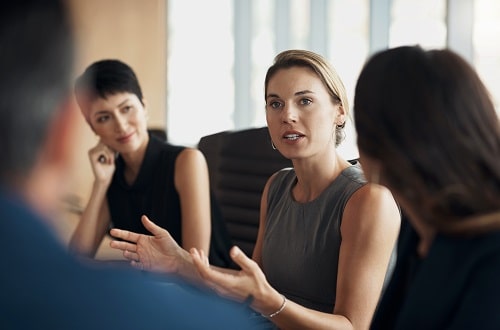
Pursuing workplace wellbeing through authentic leadership
By Dr Audrey Fleming, British Safety Council on 26 April 2024
By being open, honest and vulnerable in their interactions at work – and genuinely seeking and valuing the input of employees – leaders can develop a workplace atmosphere where trust and respect flourish, in turn supporting the wellbeing, engagement and performance of their teams.
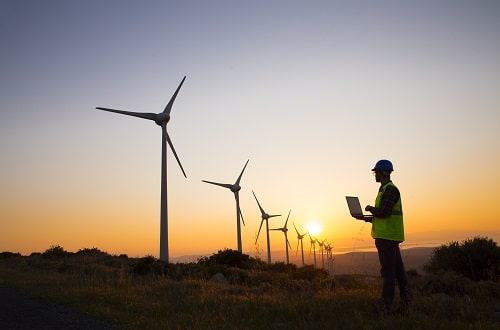
Out in the field: why lone worker monitoring is key
By Rebecca Pick, Pick Protection on 26 April 2024
People working away from a fixed base out in the field may need to quickly summon assistance in an emergency, but it’s important to choose the right communications and alarm technology for their needs.
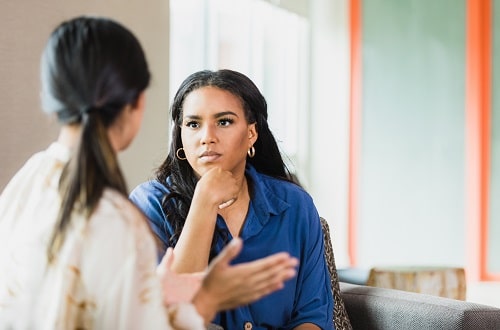
Why line managers play a vital role in workplace wellbeing
By Marcus Herbert, British Safety Council on 03 September 2023
The behaviours of line managers can have a positive or negative impact on employee health, wellbeing and engagement, so it’s vital managers get staff feedback on whether their management style is supportive or negative, and have regular check-ins so workers can raise concerns about their wellbeing.